然而,市场对个性化和定制化需求的增加,也推动了柔性生产和小批量多品种生产模式的发展。企业在优化供应链管理、提升产品质量和确保合规的同时,还需注重员工技能的提升和团队协作能力的培养,以应对新技术和市场变化带来的挑战。
尽管如此,制造企业在生产过程管控中仍面临诸多关键痛点,这些痛点需要通过全面的数字化转型来解决。
制造企业在生产过程管控中主要面临以下几个关键痛点:
⚠️ 痛点1:
生产过程监控不到位:生产过程中需要监控的指标众多,但由于监控手段和数据不完善,导致无法及时发现和解决问题。
⚠️ 痛点2:
设备维护不及时:设备维护不足或不及时会导致设备故障和停机时间增加,影响生产进度和效率。
⚠️ 痛点3:
质量管理不完善:生产质量不稳定,产品质量问题频发,难以形成从质量控制、质量追踪到质量改进的闭环管理。
⚠️ 痛点4:
生产数据难以产生价值:数据散落在多个系统中,难以进行有效分析,无法为生产管理提供有价值的支持,缺乏从决策层到各级别的数据分析能力。

为了解决上述痛点并提升企业生产管理能力,企业应通过建立数字化生产指标体系,实现全面的管理提升。
数字化生产战略:提高生产效率,提升质量水平,增强设备OEE。
生产各项业务管理:构建数字化生产管理分析体系,开发订单执行、计划管理、生产执行、质量管理、设备管理、安全管理、能耗及环保等业务看板,全面提升企业生产管理能力。
生产自助分析平台搭建,提升人效:对生产全过程业务数据进行加工,梳理生产管理分析指标,为业务人员提供拖拽式业务探索工具,提升工作效率。
完善数据底层,搭建固定报表:打通各业务系统(如ERP、MES等)数据,同步数据填报及导入,完善数据底层,根据业务需求搭建生产日、周、月报表,实现降本增效。

为了成功实施数字化生产管理,企业可遵循“三步走”的建设思路:
梳理生产分析指标体系:依托企业经营战略,梳理和确定生产分析指标体系。
搭建生产指标模型和分析平台:基于指标管理平台,搭建生产指标模型和分析平台。
构建生产分析场景:结合分析经验,构建生产分析场景,确保数据模型和分析平台的实际应用效果。
在实施过程中,思迈特软件通过访谈调研梳理客户自身的分析指标,同时结合行业经营提供建议指标,共同输出最终的指标体系。
基于生产管理分析体系,落地生产数据模型,构建以发现问题、定位问题、根因分析和业务优化为核心的四层架构,全面呈现业务全貌。涵盖制造管控中心大屏,以及订单管控、生产计划、生产效率、生产成本、设备管理、质量管理、安全管理等7个主题看板。
1、制造管控
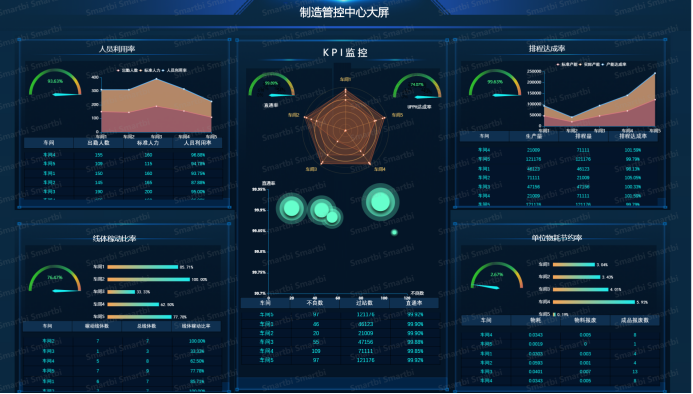
2、订单管理
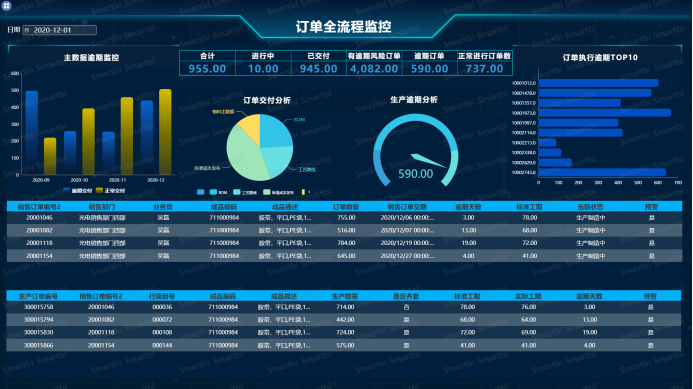
3、生产管理
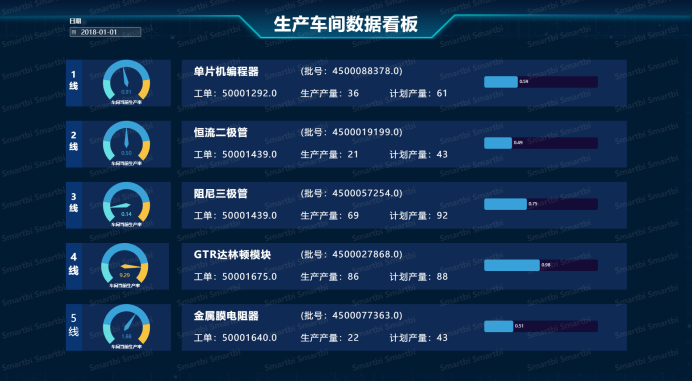
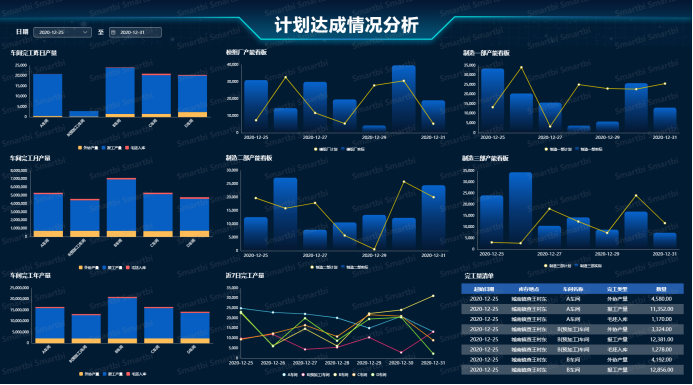

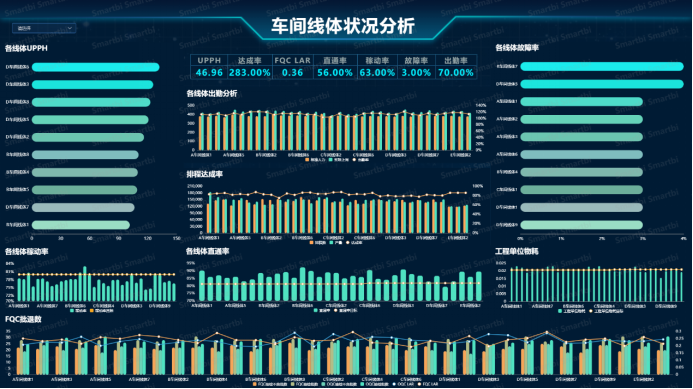
深入分析生产成本,包括成本金额、各项成本占比、直接人工、物耗及单位物耗等,明确成本结构,帮助企业识别成本高的环节并采取降本措施。
4、设备管理
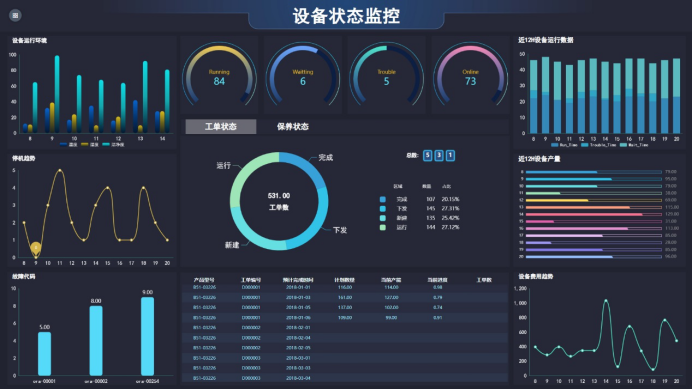
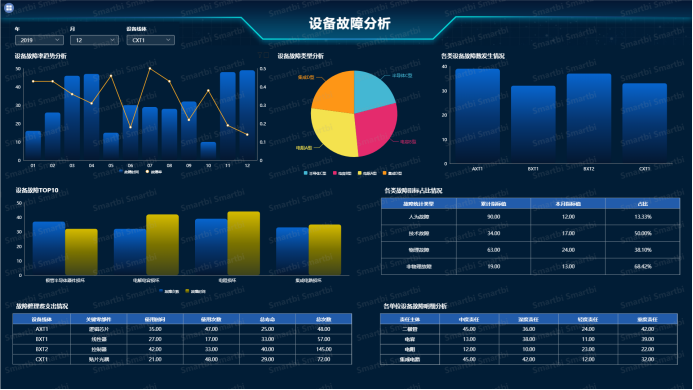
5、质量管理
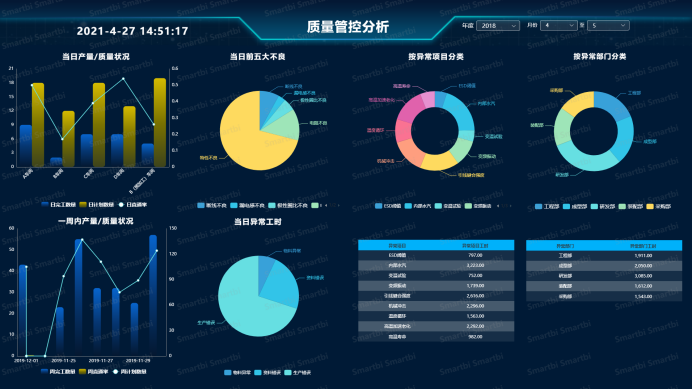
实施统计过程控制(SPC),应用统计技术评估和监控生产过程各阶段,确保产品和服务符合要求。通过及时识别生产过程中的异常因素,迅速采取措施纠正,防止不良品产生,提高整体产品质量。
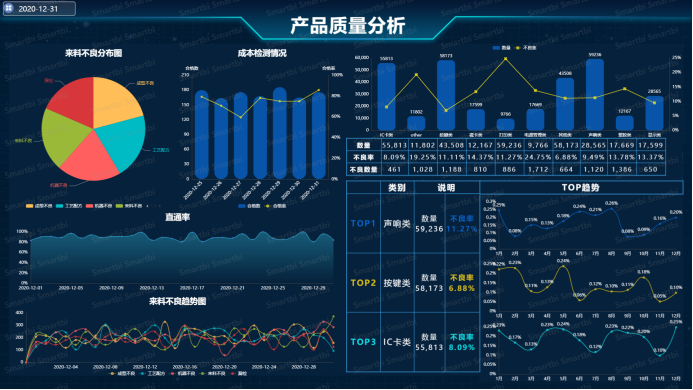
6、安全监控
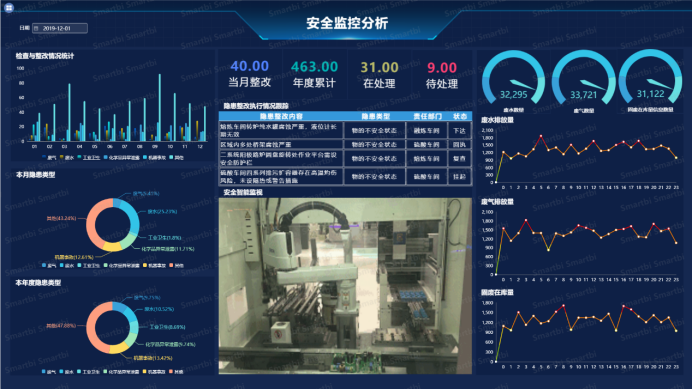
7、能耗管控

申菱环境集研发设计、生产制造、营销服务、集成实施、运营维护于一体,为全球客户提供环境调控解决方案。随着业务发展,公司在数字化升级中面临数据孤岛、手工登记、系统割裂等问题,导致数据无法集中展示和分析,难以实现实时数据洞察和敏捷决策。
为解决上述问题,Smartbi通过强大的数据接入、采集、整合、处理和建模能力,帮助申菱环境打破数据孤岛,统一整合数据。通过Smartbi搭建的生产指挥调度中心看板,实现生产全过程实时管理和运营指标监控。Smartbi的引入大幅提升了申菱环境的生产效率和经济效益,并在2022年获得标杆工厂荣誉和1500万元省级工业信息专项资金补助。
-相关资料-
-优秀制造企业的共同选择-
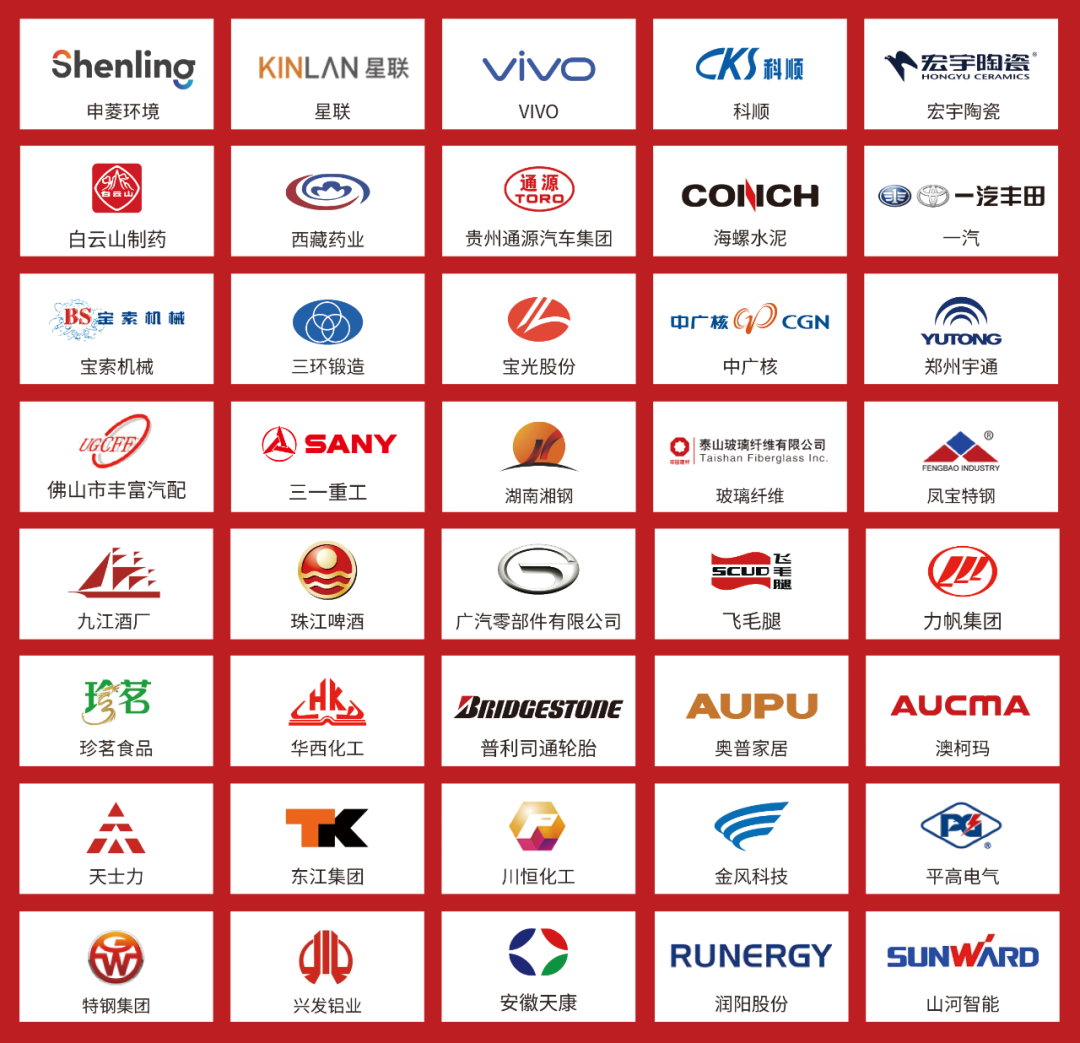